Radia mitigates WindRunner™ CO2e impact
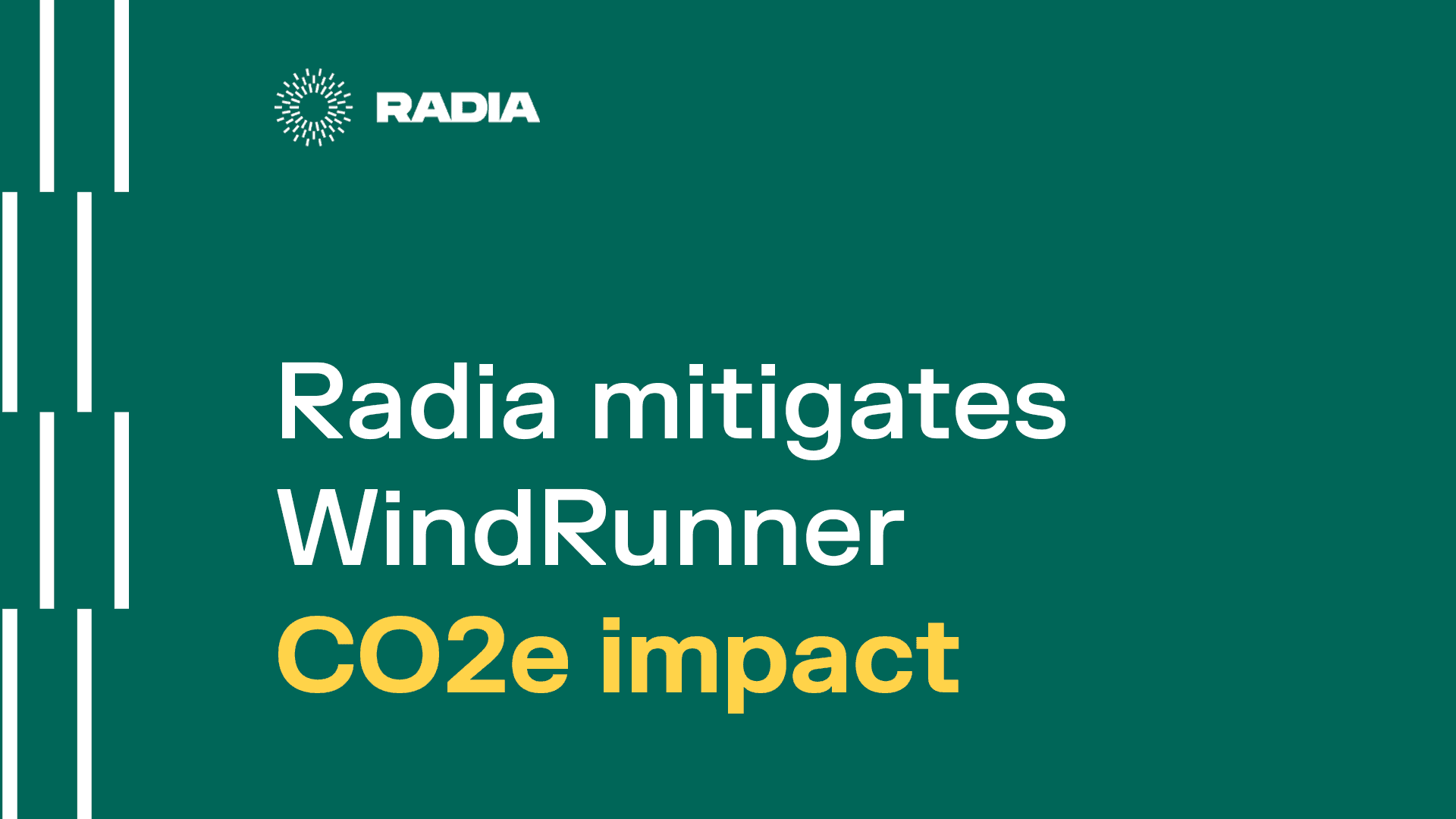
Like any infrastructure project, installing a wind farm creates a carbon footprint related to transportation, manufacturing and raw materials.
However, transportation is a negligible contributor to the carbon footprint when GigaWind™ turbines – Radia’s term for the largest onshore wind turbines of today and the even larger ones of tomorrow – are delivered by WindRunner™. In fact, transportation of wind farm components today generally accounts for only about 7% of the wind farm’s total carbon footprint. With WindRunner, that impact falls as low as 4%.
Most of the carbon footprint related to wind energy stems from the emissions embodied in wind turbines themselves. Up to 90% of the CO2e emissions associated with wind energy come from manufacturing and raw materials, including the production of steel needed to make turbine towers, composites for the blades and concrete for the turbine’s foundation. This means wind energy’s CO2e emissions impact is mostly frontloaded and unrelated to the turbine’s energy generation.
While transportation has a small impact and manufacturing and raw materials are larger contributors, GigaWind ultimately mitigates the impact of all by maximizing green wind energy output at lower cost and higher efficiency, and WindRunner is designed to operate with the smallest possible impact on CO2e emissions.
Let’s take a deeper look at how WindRunner and GigaWind have a net positive impact, both in the short term and in the complete lifecycle of a GigaWind energy project.
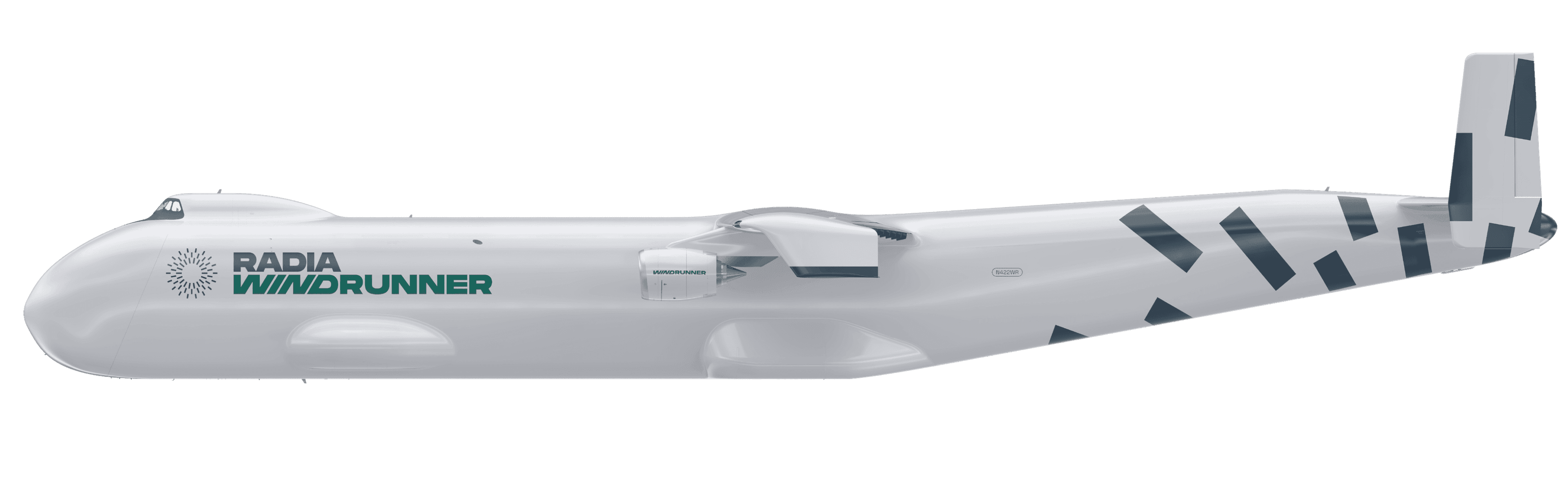
WindRunner CO2e considerations
Transporting wind turbine blades by either ground, rail, ship or air via WindRunner does create a carbon footprint – albeit one that is small compared with the carbon footprint of the wind farm, negligible compared with burning fossil fuel for power, far outweighed by the advantages of GigaWind turbines becoming operational, and balanced by other measures we have taken and will take to reduce carbon emissions of the transport of these massive blades and components.
Most importantly, WindRunner will eventually run on 100% sustainable aviation fuel (SAF) to reduce its carbon footprint.
Globally, aviation accounts for 2% of all human-caused CO2e emissions and 12% of all transportation CO2e emissions, according to the U.S. Department of Energy. When compared with conventional jet fuel, 100% SAF can potentially cut greenhouse gas emissions by up to 94% depending on feedstock and technology pathway. Thus, WindRunner will significantly reduce its carbon footprint by using SAF.
In addition to WindRunner flying on SAF, GigaWind will be used to produce green molecules, including SAF. This means Radia will help decarbonize other aerospace operations.
Of course, building WindRunner will also create a carbon footprint, just like any manufacturing process does. Radia estimates the manufacturing of each aircraft will produce about 0.002 kilograms of CO2e per megawatt hour the aircraft enables.
To help alleviate that impact, Radia will have solar panels on top of its final assembly line (FAL) facilities with the goal of being fully powered by green electricity. Its FAL will be ISO14001 certified and its tier-1 suppliers will be ISO 14001 certified. Even so, building WindRunner is still two orders of magnitude smaller in terms of CO2e emissions than building wind farms.
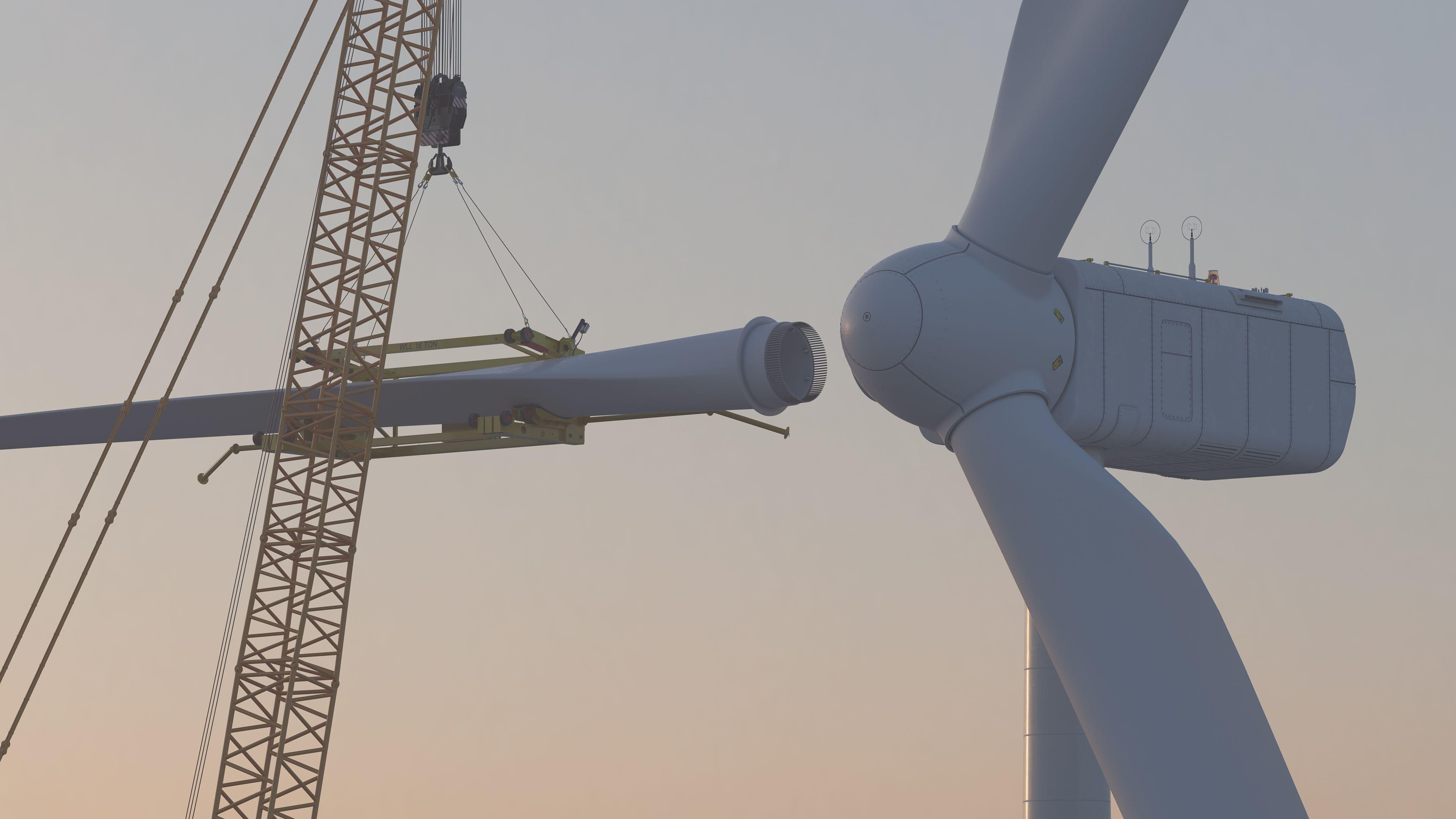
GigaWind CO2e considerations
GigaWind turbines generate more reliable, steadier renewable energy at lower cost and in large amounts – with minimal carbon emissions while in operation. These turbines require highly specialized technology, manufacturing and logistics that inherently create a carbon footprint.
However, it’s a relatively small footprint in both absolute terms and compared with other renewables, and GigaWind’s net positive impact as a renewable energy source also helps mitigate any carbon footprint WindRunner creates while transporting it.
Because they are larger and more efficient, GigaWind turbines have half as much carbon footprint impact per gigawatt as today’s smaller wind turbines. Even though manufacturers need more steel and concrete to build a GigaWind turbine, per gigawatt there is a lot less impact. Larger turbines equate to a substantial reduction in the wind farm’s CO2e emissions footprint. And over time, the initial negative impact is balanced and will indeed become net positive.
As mentioned earlier, compared to manufacturing and raw materials, transportation accounts for only about 7% of the wind farm’s total carbon footprint. When WindRunner uses SAF, that percentage drops to 4%. This includes the delivery of the turbine and its components for erection and any means of transportation used later to shuttle crews back and forth to maintain and repair a turbine over its roughly 25-year lifespan. Furthermore, GigaWind turbines reduce CO2e emissions compared with smaller turbines so much that it would still be worth transporting them with WindRunner, even if SAF wasn’t available.
Only needing to install 120 larger GigaWind turbines to generate the same energy as 200 standard-sized onshore turbines means 80 fewer foundations, 80 fewer towers and 240 fewer blades needed – again, less manufacturing means a smaller upfront carbon footprint. GigaWind’s material savings more than make up for emissions from WindRunner’s engines. Fewer, larger and more efficient GigaWind turbines create a smaller carbon footprint, while using SAF-fueled WindRunners delivers cheaper renewable energy in larger amounts.
Put simply: Wind is clean, but GigaWind is cleaner.
Finally, at decommissioning, deconstruction, and ground rehabilitation and correction, most of the GigaWind turbine is recyclable; its concrete foundation can be razed and the land can be returned to pre-construction condition.
Only WindRunner can enable GigaWind
Annual CO2e emissions for a typical GigaWind farm will total 22,400 tons, or 5.6 grams per kilowatt hour (Figure 1). That’s a 23% net reduction of CO2e emissions compared with standard wind, with WindRunner accounting for only 4.3% of that output.
As shown in Figure 1, GigaWind easily beats solar’s output of 192,000 tons of CO2e emissions and a modern combined-cycle natural gas plant’s output of 1,760,000 tons of CO2e emissions over the same period.
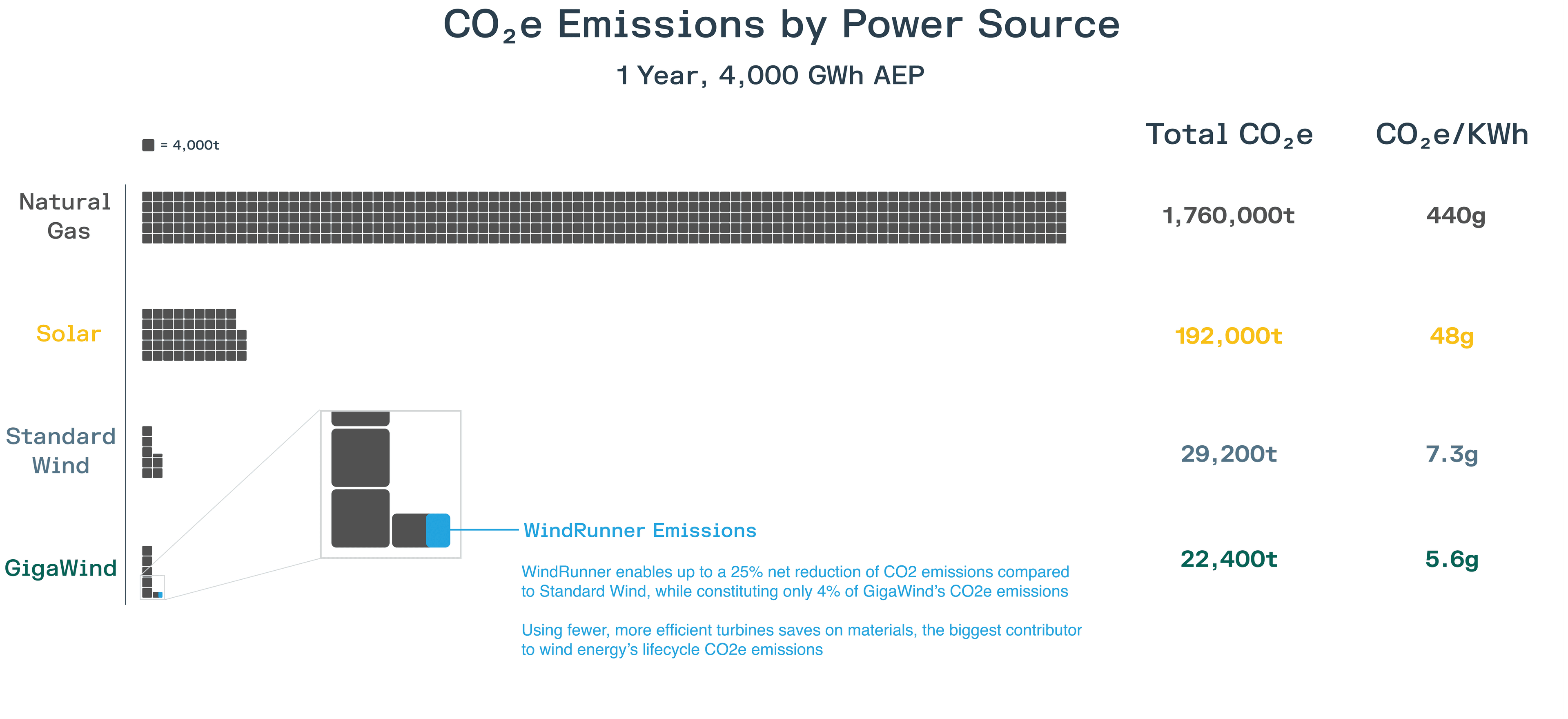
Figure 1. Lifetime CO2e emissions by power source
Enabled by WindRunner, Radia will expand wind turbine manufacturers’ existing large turbine product portfolio market and margins for both grid-connected and off-grid projects and applications, including the hard-to-decarbonize industrial sector. By taking to the skies with the smallest possible carbon footprint, Radia will bring the cheapest green electrons and green molecules to market with the urgency required to enable the energy transition.