WindRunner™: The Only Viable Solution for Enabling Advanced Onshore Wind Technologies
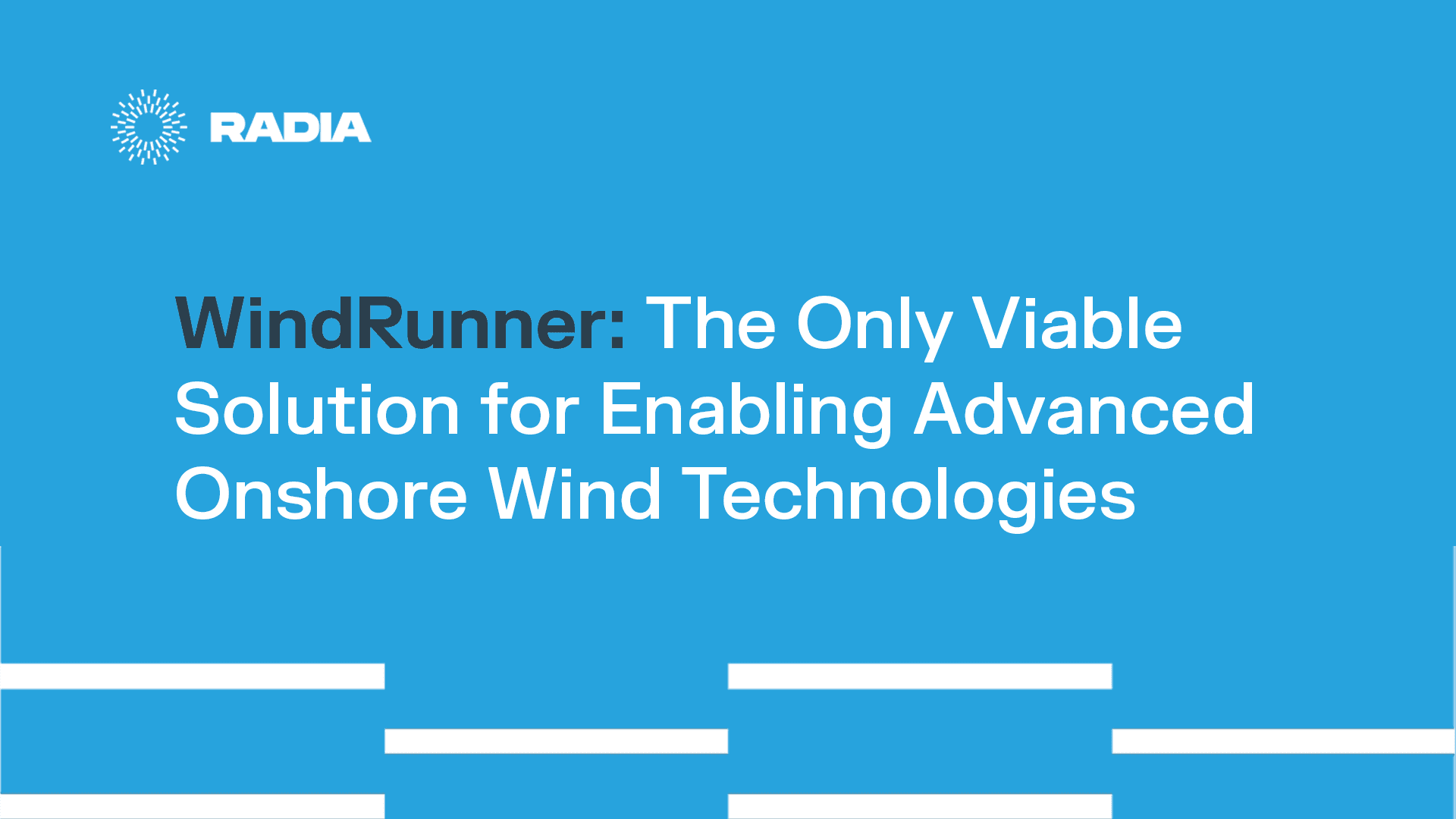
Manufacturers of today’s and tomorrow’s largest onshore turbines – what Radia calls GigaWind™ – face a colossal challenge when it comes to deployment. Due to GigaWind’s enormous size – particularly its blades – manufacturers find it practically impossible to transport these blades on the ground.
Yet, as shown in Figure 1, GigaWind – the largest, most powerful turbines ever deployed onshore – creates unprecedented economies of scale, delivering lower cost clean energy and expanding the addressable market for wind power.
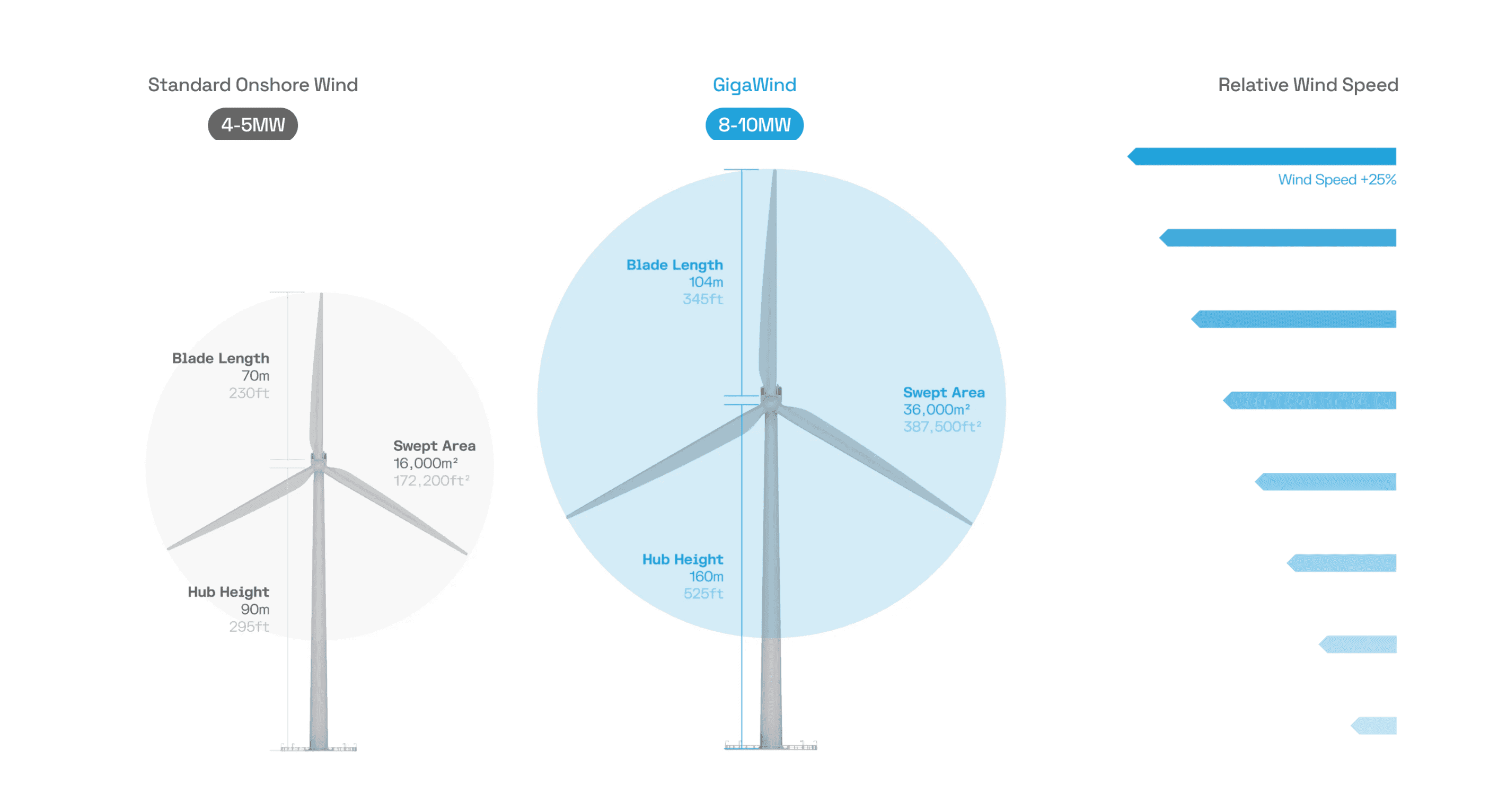
Figure 1. Radia enables GigaWind: unprecedentedly large onshore wind turbines
The three most obvious solutions currently available to get around this challenge are segmented blades, manufacturing blades onsite and aerial transport.
While on the surface these all seem like compelling options, only one can deploy GigaWind practically, economically or effectively to expand the addressable market for onshore wind power and accelerate the energy transition.
In fact, the only solution that will work for GigaWind is Radia’s purpose-built aerial transport solution, the WindRunner™ – the world’s largest aircraft.
The only solution that will work for GigaWind is Radia’s purpose-built aerial transport solution, the WindRunner – the world’s largest aircraft.
Segmented blades
Since 2005, wind turbine manufacturers have tried blade segmentation – making turbine blades in multiple pieces for easier transport with final assembly done on-site. But most have been challenged to implement segmentation practically, and the failure rate for these non-monolithic blades has been proportionally higher.
As shown in Figure 2 below, segmented blades have not been able to offer a reliable, long-term solution because of a variety of physical, manufacturing, labor and maintenance cost challenges that have proven extremely difficult to overcome. These challenges include:
- Design Limitations: By necessity, segmented blades have a heavy joint far along the span of the blade, which in addition to adding weight also means the structural load on the turbine is much higher. This necessitates further reinforcement to prevent structural failure. Compounding this, segmented blades must still fit on the roads, constraining their root diameter and chord to suboptimal aerodynamic shapes and requiring even more structural reinforcement to support the load imposed by the heavy joint with a narrower, slender blade. This means 14-16% less blade area to harness the wind resulting in a net performance loss of 3-8% – a serious penalty in an industry where a fraction of a penny per kilowatt-hour can separate the winning power auction bid from the losing one.
- Manufacturing costs: Segmented blades have more parts, use more raw materials, require more engineering and design, and require more steps and labor than monolithic blades to manufacture, making them a more expensive option on top of performing worse than an equivalent monolithic blade. Higher manufacturing costs mean a higher cost per unit of electricity generated, undermining the benefits of bigger turbine blades in the first place.
- Labor costs and construction delays: Segmented blades must be assembled in the field at the wind farm site, which removes all the advantages of assembly in a controlled environment by a full-time, experienced and highly skilled labor force using dedicated equipment. It’s often difficult to find a local source of labor with the skills required to properly assemble a segmented blade in the field, introducing risks surrounding labor availability and quality control. Moreover, additional construction steps mean a longer time to complete wind farm construction, giving more opportunity for costs to pile up and pushing revenues further into the future.
- Failure risks and higher maintenance costs: Made of composite materials, all turbine blades are designed to survive two or more decades and tens of millions of load cycles in the harshest environments. Compared to a passenger jetliner’s wings, which must survive 10,000 to 100,000 load cycles in their service life, the durability requirements for wind turbine blades are extreme. Blade segmentation introduces a critical failure point in these carefully designed and constructed components. The failure of this joint in any one of these millions of load cycles means at best an inoperable turbine until the blade can be replaced at great expense, or at worst a catastrophic failure that destroys the entire turbine. Because of these risks, segmented blades must be inspected and maintained more often, adding additional operating costs and potentially even shortening the overall lifetime of the wind farm.
In sum, due to the impaired performance, higher costs and elevated failure risks associated with segmentation, monolithic blades are simply better at meeting the demanding requirements wind turbines face. In the end, these issues with segmented blades impose penalties on LCOE and ultimately detract from the advantages bigger blades offer.
Manufacturing blades onsite
Wind turbine blades are the largest composite objects ever made.
The factories that build turbines are highly advanced and staffed by skilled workers in controlled environments to facilitate this incredibly precise and painstaking manufacturing process.
The best way to lower costs and produce more advanced technology is by consolidating production to fewer, more sophisticated factories that can provide the ideal environment for producing components reliably, efficiently and quickly while also being tightly integrated with the downstream and upstream supply chain. Because of this, the last 20 years have seen substantial supply chain consolidation to exactly this model in the wind industry.
By contrast, as shown in Figure 2 below, efforts to manufacture wind turbine blades at the wind farm would add enormous amounts of additional complexity, risk and cost to this process.
Aerial Transport
The clear solution, then, is to simply fly around all the terrestrial logistical limitations faced by GigaWind specifically and all onshore wind generally. But how? While some historical or existing options like airships or helicopters may seem appealing, the only realistic solution is a purpose-built, fixed wing aircraft designed for the wind industry.
Let’s explore.
Aerial Solution Option 1: Buoyant Aircraft (Blimps)
Consider airships or other buoyant aircraft designs, like blimps. On the surface, they seem like a charming and viable solution. But dig deeper, and the risks and difficulties become more apparent.
Traditionally, airships have struggled to lift heavy objects because the earth’s atmosphere isn’t dense, relatively speaking, and buoyant gases like helium don’t generate enough lift to transport super-heavy objects until the aircraft in question is as large as a football stadium. Such huge proportions create tremendous amounts of drag when moving through the air, which makes airships very slow and therefore operationally inefficient. Due to their slow speed, airships have very low throughput, meaning they would only manage a handful of deliveries a month, which in turn means there are fewer missions to amortize the $200 million to $300 million cost to build such an aircraft.
Managing buoyancy when transporting heavy objects is also a technical challenge because a blimp or airship dropping off a 45-ton turbine blade must have an equal amount of ballast on hand during the operation to remain neutrally buoyant, or else it will begin to ascend rapidly and uncontrollably after releasing its payload.
While they don’t require runways to take off and land, buoyant cargo airships do require a circular area with a diameter equal to four times the length of the airship. For the football-stadium sized aircraft contemplated above, that means a cleared area of about 150 acres, or 60 hectares. On top of that, they are also highly susceptible to crosswinds and weather, grounding them more frequently than fixed-wing aircraft because of the inherent danger of operating them in even moderate wind conditions. Notably, wind farms tend to be in areas with high wind.
For example, a modest crosswind of 35 km/h renders an airship virtually uncontrollable for a precision landing due to its enormous size and neutral buoyancy. And due to their slow speed, a headwind of this magnitude can cut their ground speed by up to a third, substantially increasing an already long mission time. Even worse, airships’ low operating ceiling means they cannot simply fly higher to avoid the weather and winds on the way, as their gas bags would rupture if they climbed high above the clouds.
Compounding all these technical and operational challenges, there’s practically no industrial infrastructure to support cargo airships. Off-the-shelf parts for lighter-than-air vehicles aren’t widely available, there is no robust and dedicated supply chain for them, and there isn’t a labor force to design, build, operate and maintain them. Additionally, there are very few dedicated hangars and physical plant facilities in existence for these types of aircraft. Building new infrastructure for them would be extremely costly.
Then there’s the issue of government certification and regulation, which for buoyant aircraft hasn’t been meaningfully updated or changed since before World War II. Even if it were a priority for regulators, it would take years for bureaucracy to devise and agree on the rules and regulations required to ensure the safe design and operation of modern cargo airships.
Put simply, buoyant aircraft have serious technical and operational limitations that have seen them supplanted totally by fixed wing and rotary wing aircraft – which also means the buoyant aircraft industry hasn’t existed at scale for 70 years and doesn’t have the vast network of skilled labor, suppliers, technology and infrastructure to make it a viable option for the 21st century.
Aerial Solution Option 2: VTOL Aircraft (Helicopters)
At first glance, vertical take-off and landing (VTOL) aircraft, like helicopters, seem like a good option. However, the immediate problem is that there are none currently in operation or planned that have sufficient payload capacity to lift a heavy wind turbine blade.
The deeper problem is that VTOL capabilities are limited by significant speed and range penalties, and transporting wind turbine blades in particular presents unique operational and safety challenges. In simple terms, needing to generate all their required lift with only engine power and not forward airspeed means VTOL aircraft use tremendous amounts of energy to simply stay aloft, enormously limiting their range and endurance while also preventing them from easily carrying heavy payloads due to their insatiable thirst for fuel. A helicopter or other VTOL aircraft with the power to carry a wind turbine blade would still suffer from these fundamental limitations.
Setting this aside, even if there were a VTOL aircraft powerful enough to lift a wind turbine blade, carrying it underneath the helicopter or similar vehicle is extremely dangerous. If there is a wind gust, the blade will do what it is designed to do and react to the wind, pulling on the aircraft and resulting in an emergency jettisoning of the blade or even a crash. This risk also makes a VTOL aircraft too dangerous to operate on all but the calmest of days, a condition that wind farms are not typically known for. Even on a calm day, safely depositing the blade on the ground would be a very difficult operation requiring extremely skilled piloting.
A vehicle of this size would also generate massive downwash from its rotors. As a result, the aircraft would kick up debris that would almost certainly pit and scour the blade’s surface, seriously damaging it before it can even be installed.
Theoretical mega-heavy lift helicopters notwithstanding, using multiple existing helicopters together also wouldn’t work. Both the U.S. and former Soviet Union experimented with tandem-lift techniques with multiple helicopters to lift heavy payloads and quickly and decisively found it too difficult, impractical and dangerous.
Ultimately, VTOL aircraft’s limited capabilities make them ill-suited to the mission of delivering GigaWind blades, even if one of sufficient size existed.
Aerial Solution Option 3: Modify Existing Fixed-wing Aircraft
Currently, a variety of fixed-wing cargo aircraft capable of moving outsized payloads operate around the world, including the Airbus Beluga and Beluga XL, Boeing Dreamlifter, Antonov An-124, and Lockheed C-5 Galaxy.
Although they are large by almost any standard, these aircraft aren’t nearly large enough to transport GigaWind blades, with none able to house a payload longer than 50 meters. Further, modifying them to be larger is also not practical. Generally, an aircraft has a maximum allowable overall weight. Modifying the fuselage length to accommodate bigger turbine blades cannibalizes weight that could be used for fuel and the payload itself, reducing operational capabilities. This means designers would quickly reach a crossover point where making the aircraft big enough to accommodate a GigaWind blade would increase the overall weight to such an extent that there would no longer be sufficient payload mass to carry the blade at all.
Even if the challenges associated with enlarging the fuselage were solved, these aircraft already require long paved runways, making them unable to deliver onshore turbine blades to the remote places where wind farms need to be constructed. Moreover, an existing aircraft with an enlarged fuselage would likely have even worse field performance than its parent design and be at greater risk of scraping its tail on the ground on takeoff or landing due to its greater length.
Moreover, there aren’t even enough of these aircraft to deliver the number of turbines with the frequency needed to enable wind power as a significant renewable energy source for a carbon-free world. For example, there are currently only four Belgua XLs in operation with a total of five planned, while only a handful of aging Antonov An-124s are available for commercial charter work.
All this means that simply extending an existing platform doesn’t work. The most pragmatic and technologically conservative approach is to create a new aircraft that is purpose-built for enabling GigaWind.
As also shown in Figure 2 below, blimps, existing cargo planes and helicopters cannot deliver the heavy wind-turbine payloads safely or cost-effectively or to the places onshore wind turbines must go.
WindRunner: The Only Solution
Radia is designing a unique, scalable aerial transport solution for the wind industry – WindRunner. When it takes its first post-EIS flight in 2029, WindRunner will transport manufacturers’ largest turbines around the world directly to windfarms that cannot be reached terrestrially or aren’t economically viable to maximize green wind energy output at lower cost and higher efficiency.
To carry the largest payloads ever moved by air, WindRunner has a cargo bay volume of 272,000 cubic feet, a wingspan of 261 feet and an overall length of 356 feet. Compared with a Boeing 747-400F, WindRunner has 12 times the payload volume, a 20-foot longer wingspan and is 127 feet longer. But while the 747 needs a runway at a traditional airport that is at least 9,500 feet long to take off and land, the WindRunner needs only about 6,000 feet on a semi-prepared landing strip at a wind farm to deliver its payload. It can deliver the largest turbines of today and the future almost anywhere in the world.
By being purpose-built to enable GigaWind, the WindRunner aircraft can emphasize simplicity and reliability in its design, flight systems, operations and manufacturing to ensure it can meet the needs and challenges of the rapidly growing wind industry. By leveraging the vast network of suppliers and parts that already exist and conforming to the latest regulatory guidance, Radia can quickly and cost-effectively deliver an aircraft that will safely and reliably enable GigaWind the world over.
As shown in Figure 2, WindRunner’s unique design makes it the only logistical method than can deliver GigaWind efficiently and practically.
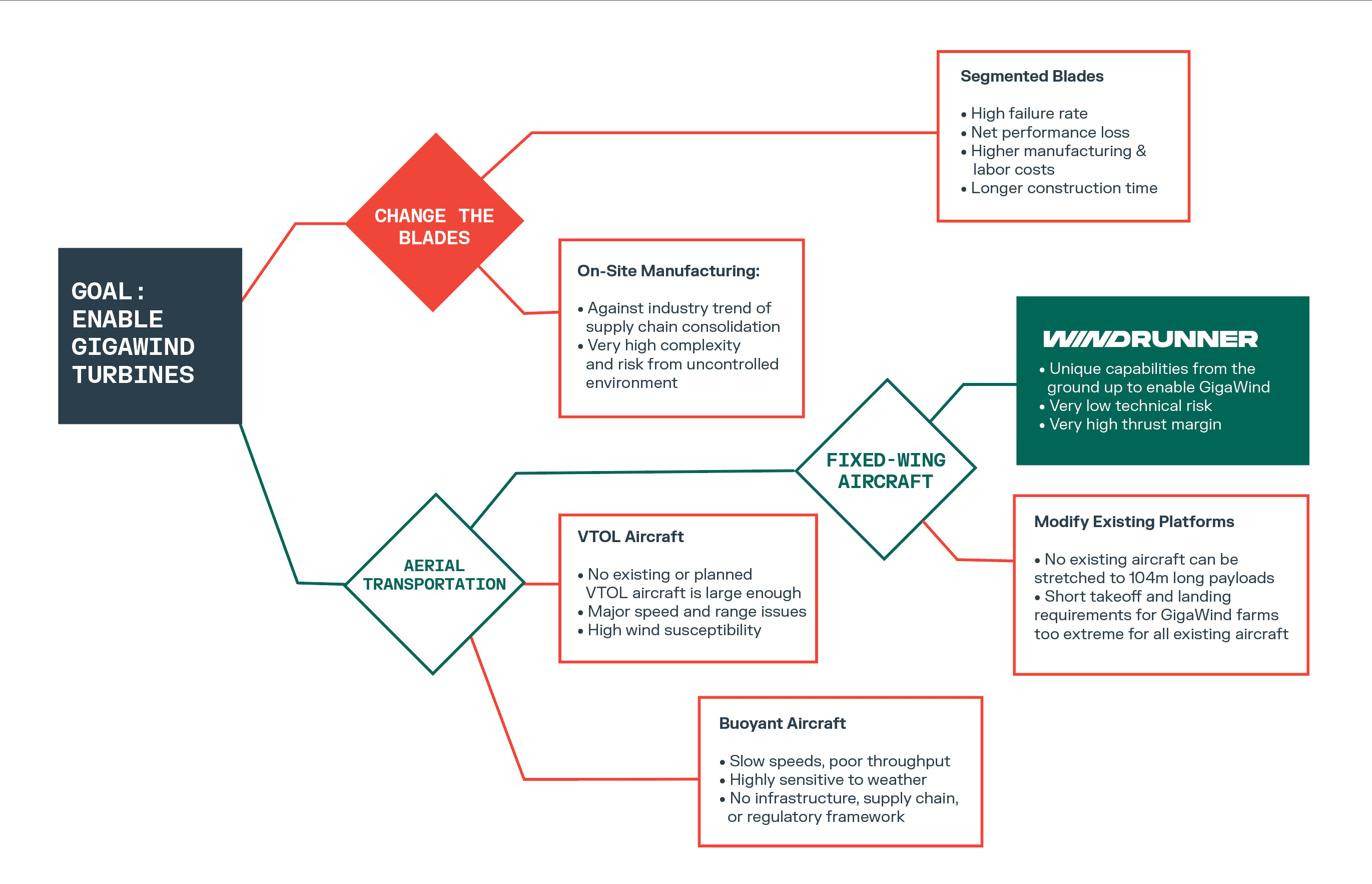
Figure 2. WindRunner is the only solution
Radia’s efforts to solve these critical issues using the WindRunner have not gone unnoticed by the wind industry. In fact, Radia has partnered with the world's top turbine manufacturers to bring GigaWind to market. Together, our partners represent the majority of the world's overall global market share. Of all the possible solutions, they’ve chosen Radia.